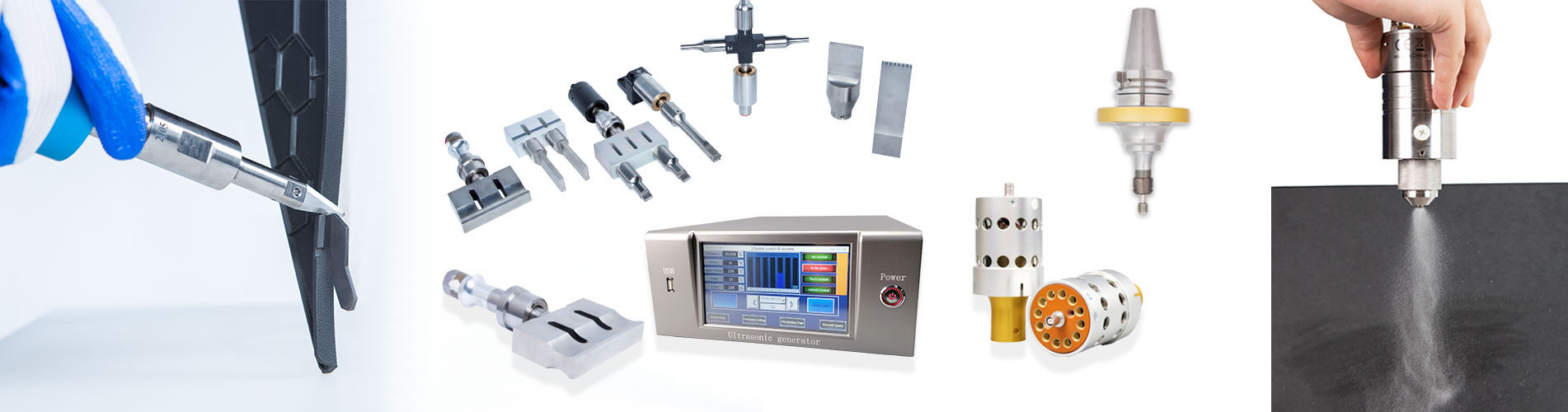
Features and advantages of ultrasonic wire harness welding machine
Compared with ordinary motors, the transducer has two main differences: First, the transducer converts electrical energy into linear vibration instead of rotation; secondly, it has a very high working efficiency and can convert 95% of the electrical energy. After being converted by the transducer, the mechanical energy is applied to the welding head. The ultrasonic welding head is made of titanium alloy and processed into a specific shape according to the principle of acoustics, thus ensuring the maximum transmission of energy.
advantage
One of the most important advantages of ultrasonic welding is the lower temperature. The generation of temperature is inevitable, it is only caused by friction, which is only 1/3 or 1/2 of the melting point of the metal. At the low temperature generated by the welding process, the metal wire retains its original performance due to annealing and the low temperature does not damage the insulation of the wire; in addition, the lower temperature also means that thin metal can be welded to thick metal Without causing damage to thin metal. These are very important in wire harness production.
Most of the metals used in electrical products have good thermal conductivity, which makes it difficult to weld by melting. Because the heat is quickly dissipated from the metal surface, it is necessary to apply more heat to complete the welding. Ultrasonic welding has not encountered these problems. In fact, since no melting occurs, the energy of ultrasonic welding is only 1/30 of that of resistance welding. In other words, the ultrasonic welding machine with a power of 3KW can complete the work that the resistance welding needs 90KVA to complete, so the cost of the work is also obvious.
Ultrasonic welding is a mechanical process, no current flows through the workpiece, so the conductivity of the metal has no effect. Contaminants and oxide layers are usually attached to the metal surface. Ultrasonic welding is used. There is no need to pre-treat the metal surface. Ultrasonic vibration can directly shake the attachments and remove them. Another important advantage of ultrasonic welding is the long life of the workpiece. The welding head of the ultrasonic wire harness machine has 4 working faces, which reduces the maintenance cost of the later equipment.
© Copyright: 2024 Hangzhou Altrasonic Technology Co.,Ltd All Rights Reserved
IPv6 network supported
Scan to WhatsApp