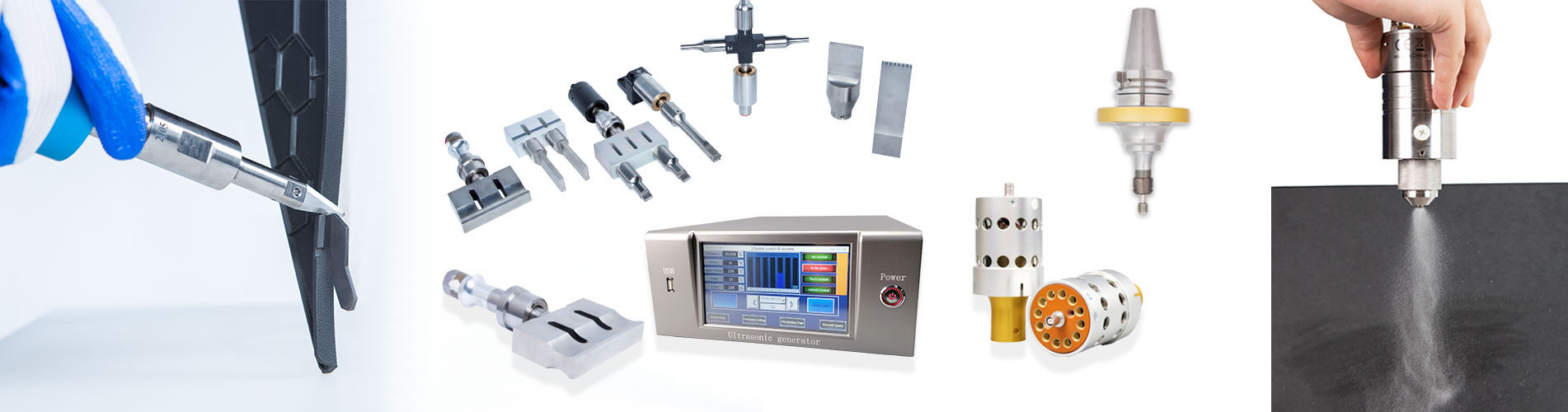
Solder a drilling tool onto the horn
Solder a drilling tool onto the horn
1. Apply a little flux and silver solder onto the end of the drilling tool.
2. Put the drilling tool into position on the horn, and add flux to the joint.
3. Heat the horn with the gas torch, until the silver solder fuses and connects both pieces.
4. Do not heat exactly at the joint of tool and horn, but below on the horn.
5. When the drilling tool is consumed during the drilling operation, the old tool should be removed by heating, and then replaced with a new tool.
Making one or two 1.5 mm holes near the upper end of the drilling tool, near the horn, is very effective for core drilling of large holes over 8 mm in diameter. The grit will also enter the
inside of the drill tube.
It is important to solder the tool onto the horn correctly, please refer to the following figures.
Small tools up to 1.2 mm are made of high carbon steel wire. As the diameter of the tool increases, machining efficiency will decrease. Therefore stainless steel tubes are used to drill holes larger than 2 mm. Wall thickness of the tube is between 0.1 to 0.5 mm
The horn needs special care.
1. Do not overheat the horn.
2. Do not quench the horn in water after soldering. No rapid cooling, as the silver solder will become brittle.
3. Do not hammer, file, drop or deform the end of the horn.
4. Excessive solder may run down along the horn, it must be removed.
5. If you file away excessive solder great care must be taken not to damage the horn.
Even a small flaw will prevent the horn from correct ultrasonic vibration and eventually breaks the horn.
© Copyright: 2024 Hangzhou Altrasonic Technology Co.,Ltd All Rights Reserved
IPv6 network supported
Scan to WhatsApp