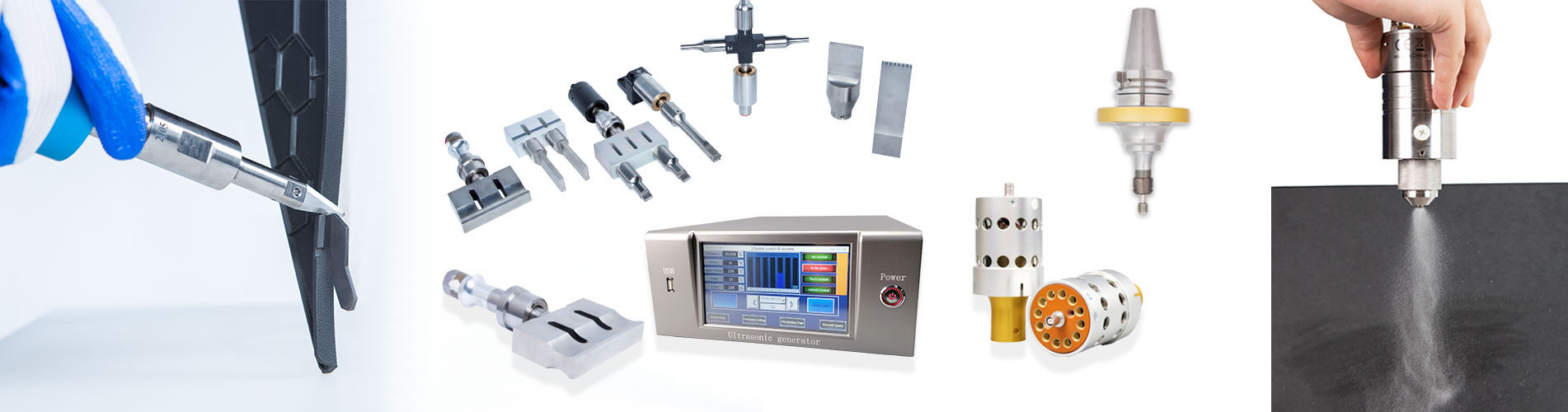
Sonotrode Design Is Key to Success of Ultrasonic Welding of Automotive Assemblies
areas might remain cold and will not bond homogeneously. With vibration welding, additional plastic is needed in the joint area. As a result, a large amount of molten material is produced during welding. This material could get pushed out of the joint, creating an unsightly bond line
Advantages
Ultrasonic welding is also subject to such physical limitations when joining complex 3D-shaped parts. However, if the sonotrode is correctly dimensioned through the use of finite element analysis (FEA), ultrasonic welding offers numerous advantages:
· Uneven asymmetrical geometries can be welded.
· Delicate component surfaces stay mark-free.
· Short weld cycles between 100 and 300 milliseconds.
· Targeted energy input protects sensitive electronic elements.
· Different types of material can be welded or bonded by embedding.
· Smaller machine footprint compared to other joining processes.
· To give engineers an idea of the importance of sonotrode design to successful welding, this article examines three recent applications involving automotive assemblies.
In one application, Herrmann was tasked with welding aluminum-coated insulation panels for the engine compartment. The material combination was a killer: Aluminum-coated polyurethane (PU) acoustic mats had to be bonded to glass-fiber reinforced polypropylene (PP) panels. If that wasn’t enough of a challenge, six different parts had to be welded.
This application represented a real challenge for permanent and safe joining of the components. Adhesives would not work due to cost considerations and the combination of materials. Clamping elements or screws were too risky, because they could become loose during motor operation. None of the other thermal joining methods, such as laser welding, infrared welding or vibration welding, were suitable.
Initial tests using a handheld ultrasonic welder proved positive. A tight joint could be created between the PU mat and the injection-molded PP part, despite the intervening aluminum layer. It was possible for ultrasonic vibrations to penetrate the aluminum coating and energize the molecules in the PP part.
The task then became how to obtain repeatable weld results and ensure the customer’s tensile strength requirement of at least 50 newtons per weld spot. Wear-resistant hardened steel proved to be the right material for the sonotrodes. Herrmann engineers determined the weld spot locations and designed the complex fixtures, including the clamping system and part scanning sensors.
The sonotrodes were mounted to pneumatic actuators attached to six-axis robots. Six different fixtures were designed to match the part shapes and to support the weld spots.
Assembly takes place on rotary indexing tables. In two positions, assembly is done by two robots. At a third position, another robot automatically loads and unloads the parts.
Valuable time—up to one second per weld spot—was saved by preloading the pneumatic cylinder that extends and retracts the ultrasonic stack. Preloading means that the cylinder has already been extended via an intelligent pneumatic system before the robot brings the weld tool in contact with the weld spot.
Another application involved the assembly of daytime running lights. A clear plastic lens had to be welded to a plastic body with a hermetic seal. The complex 3D shape and class A surface were a challenge to weld. The customer also needed a cost-efficient system that could accommodate many variants for various car models.
To solve the problem, we developed a composite sonotrode separated into two elements: a carrier-block sonotrode and a number of individually screwed-in tips. Each tip is a different height to fit its lens exactly.
To guarantee correct vibration, the carrier sonotrode was designed with the help of FEA and tuned for the correct frequency, idling power and amplitude. In addition, each tip was designed, manufactured and tuned like a stand-alone sonotrode. The tips include features for various interfering contours. For instance, some tips have cutouts to accommodate raised lettering on a component. All this influences how the sonotrode vibrates.
To ensure that the tips vibrate correctly, they were individually tested and adjusted in a pains-taking and time-consuming manual process. Under load simulation, the completed composite sonotrode was laser-measured and any corrections were performed by CNC machining. Special software measures up to 100 points to create the amplitude profile. Once calibrated, the composite sonotrodes worked beautifully and have been sold repeatedly.
To assemble model variants, all parts of the ultrasonic system form a “quick-change tooling frame” that can be detached from the main machine and exchanged with a different frame. During the startup phase, assembly was performed with one machine and multiple tooling frames. As variants increased, the customer only needed to purchase additional tooling frames. Cost-intensive components, such as ultrasonic generators, controls and safety systems, can be used with multiple tool frames for various daytime running lights.
One more application involved bonding pressure-balancing membranes to pump housings. The housings are made of glass-fiber-reinforced polyphenylene sulfide (PPS). The membranes are made of polyester or polycarbonate. The customer wanted to replace expensive precut single membranes with less costly membrane tape.
This was a demanding application, because three consecutive ultrasonic process steps had to be performed:
· Punching out the membrane and welding it to a cap (35 kilohertz).
· Providing the cap with a protective cover (35 kilohertz).
· Welding the complete cap to the casing (20 kilohertz).
Our newly developed ultrasonic tool system, MPW, does just that. It punches and seals at the same time using a membrane tape on a roll, saving money
© Copyright: 2025 Hangzhou Altrasonic Technology Co.,Ltd All Rights Reserved
IPv6 network supported
Scan to WhatsApp