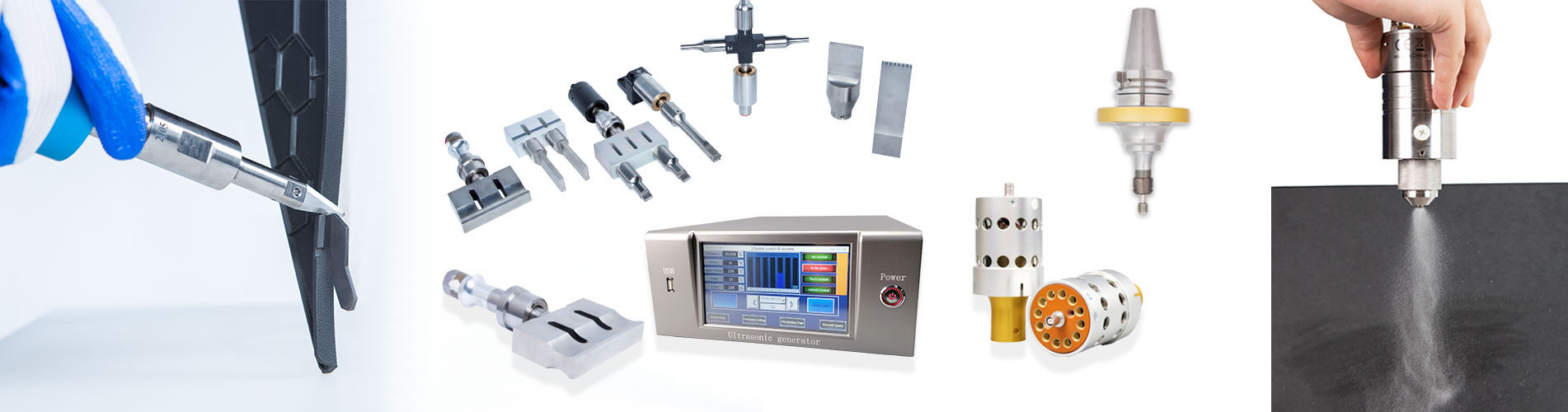
The Lithium Ion Inflection Point
Rechargeable lithium ion (Li-ion) batteries were first developed as a commercial product by Sony in 1991, to solve a specific problem with the company’s video cameras. The typical video camera of the time had evolved from a professional beast that sat on the videographer’s shoulder to something that could fit into the palm of the hand, but the nickel cadmium batteries that were available were so large that the devices had an unsightly and hard-to-hold bulge thanks to the bulky battery pack.
Sony needed a battery that held enough energy to run the camera but was small enough to match the camera. Battery life wasn’t all that important, as few video cameras of the day were used for more than 100 hours per year, and they were recharged, on average, fewer than ten times during that period.
So Sony turned to the only battery chemistry that offered the required energy density and form factor: lithium ion. The very first lithium ion battery was created in an Exxon laboratory by Dr. Stanley Whittingham and his team. Dr. John Goodenough, an electrochemist at the University of Texas, refined the chemical inputs to lay the foundation for the modern lithium cobalt cathode (which is still used in almost every consumer electronic and power tool battery today). Then Sony created the first mass manufactured lithium ion battery to solve its video camera problem.
Soon after that, lithium ion batteries started doing what they would do in multiple other sectors since then: replace the incumbent chemistry. By the mid-1990’s, almost all cameras with rechargeable batteries were using lithium ion. They then took over the laptop battery market and — shortly after that — the nascent cellphone market. The same trick would be repeated in tablet computers, power tools, and handheld computing devices.
Today, Li-ion batteries are on the verge of their greatest market disruption yet: the energy sector. We are entering an age where Li-ion batteries will become an integral part of both the electric power grid and the automobile industry. This is already happening in niche applications, and will soon move to the mass market as well. When it does, the Li-ion industry will transform from a relatively minor player, concentrated in consumer electronics, to become a foundation of the global economy.
This inflection point is based on manufacturers reaching critical goals in three different but interwoven specifications: durability, safety, and, most importantly, cost. Traditionally, a battery manufacturer could alter the ingredients or the manufacturing process in order to improve one of those specifications ‑ but now the industry has reached a level of sophistication where all three are improving simultaneously.
The durability requirement is different from what it was when Sony made the first batteries for video cameras. In order to penetrate the electricity and transportation sectors, a battery has to lose 20 percent or less of its capacity after 10 years of constant use. The conventional lithium cobalt cathodes in the consumer electronics industry weren’t capable of doing that. And they didn’t need to be when they were being put into phones and computers that weren’t expected to last more than three years. Cars and electrical substations, however, require much longer operational time frames. That’s why new variants of the lithium cobalt cathode, such as nickel cobalt aluminum (NCA) and nickel manganese cobalt (NMC), are being used in power grid systems and in electric vehicles, such as the Tesla Model S. While these batteries still contain cobalt (usually the most expensive chemical input into a battery), they promise a much longer lifetime (the number of years a battery will last regardless of the usage pattern) and cycle life (the number of charge/discharge cycles a battery can endure before it has significant degradation). Other new cathode chemistries, such as lithium manganese spinel (LMO) and lithium iron phosphate (LFP), are much longer-lived than their consumer electronic predecessors.
The issue of safety is also a crucial one for batteries to become more widely used for energy applications. Any form of energy storage, whether a flammable battery or combustible gasoline, has an inherent safety risk. Batteries must reach especially high levels of risk mitigation before mass consumers are comfortable with them. Cellphone owners are comfortable with the safety risks of a lithium ion cellphone battery (which, in truth, are minimal) because a catastrophic failure will leave, at worst, a nasty burn mark. The sheer volume of batteries required in EVs (the Tesla Roadster, for instance, has more than 8,000 individual cells in it) and power grids, though, means that the consequences in the case of catastrophic failure would be much graver. Even relatively harmless “smoke conditions,” such as the short circuit of batteries on the Boeing 787 Dreamliner prototypes, can be public relations nightmares that can cost a company billions of dollars in lost sales. Thus safety engineering is crucial. And thankfully, the newer generation of chemistries is up to that task: if you pound a nail into an LFP battery, for instance, the only negative consequence you get is a dead battery.
The biggest limiting factor in lithium ion batteries for the last few years has been price. In 2009, Navigant Research estimated that new LFP or LMO batteries, purchased in volume, probably cost about $1,200 per kilowatt-hour (kWh). Today that price has dropped to around $500 per kWh. This is due to three interrelated phenomena: manufacturing scale, manufacturing efficiency and supply chain maturity.
The sudden increase in scale of manufacturing for next-generation Li-ion batteries was greatly aided by the economic crisis of 2007 to 2010. Government funding programs in China, South Korea, Japan, and the United States provided enormous subsidies to build new battery plants in those countries. All told, there are now more than 50 gigawatt-hours of battery manufacturing capacity throughout the world, more than three times the 2007 level.
Factories, by themselves, don’t build anything. For them to function effectively, line workers and managers must be able to learn to manufacture high quality items quickly and cleanly, in order to make money at making things. That learning process has been going on for more than two decades in the consumer electronics battery business, and an iterative process of manufacturing efficiency gains has led to extremely cheap prices for those batteries. Five years ago, a laptop battery cost more than $1,000 per kWh when ordered in bulk. Today, that price is closer to $250 per kWh.
The same efficiency improvements have been happening for the last 3 years in factories producing the newer versions of Li-ion batteries. As manufacturing yields increase and waste decreases, these batteries will get even cheaper to make.
The third leg of the cost reduction stool for advanced Li-ion batteries is the development of a mature supply chain. The various solvents, chemical precursors (such as lithium carbonate), and other components (metal enclosures, plastic separators, copper wires, aluminum anode plates, etc.) were specialty batch-processed orders five years ago. Today, they are becoming bulk commodities that are manufactured more cheaply in continuous processes. Additionally, the transportation channels that get these supplies to the battery factories are well determined and logistically simple. As this supply chain maturation continues, the batteries will get even cheaper.
So how inexpensive can these batteries get? According to the Navigant Research report, Emerging Battery Technologies, large-format Li-ion batteries, made from the newer generation of chemistries, will decline from around $500 per kWh today to around $300 per kWh in 2015. At that point, the price curve should follow the well-worn path of the consumer electronics Li-ion battery pricing decline. By the time that the two industries are equal in size, the newer chemistries will be even less costly, because of their larger formats (a larger battery means less inactive material for a given energy storage capacity) and the lack of cobalt as a material input in most newer Li-ion chemistries. Cobalt is not only much more expensive than any other chemical input, but it also often comes from conflict-scarred regions of Africa. Eliminating the need for cobalt will dramatically lower the battery price.
By 2020, Navigant Research expects that prices for batteries will be below $200 per kWh. At that point, EVs will carry only a small premium over their gasoline counterparts, and battery-based energy storage will be almost as inexpensive as natural gas generation in a peaker plant. When those milestones are achieved, the battery market will become worth more than $75 billion in annual revenue (as opposed to about $12 billion today).
But the inflection point for dramatic growth will happen much sooner than 2020. In fact, it’s already happening today. Batteries can provide ancillary services for the power grid today in such a way that running a business off of operating large-scale battery banks can be profitable. The biggest money-making application today is frequency regulation, an ancillary service for the power markets that uses micro-pulses of energy to maintain the proper frequency of the current on the grid. According to the Navigant Research report, Energy Storage Systems for Ancillary Services, more than 100 MW of batteries will be installed in the United States in 2013 for frequency regulation, which will more than double the installed base of grid batteries in this country.
In the transportation sector, meanwhile, the Tesla Model S (which is powered exclusively by Li-ion batteries) already outsells its more traditional luxury rivals, such as the Audi A8 and Mercedes E Class. If Tesla reaches its goal of 50,000 annual sales of the Model S in 2015, that model alone will account for more battery capacity than all the batteries in new laptops, tablets, and cellphones sold that year combined.
© Copyright: 2024 Hangzhou Altrasonic Technology Co.,Ltd All Rights Reserved
IPv6 network supported
Scan to WhatsApp