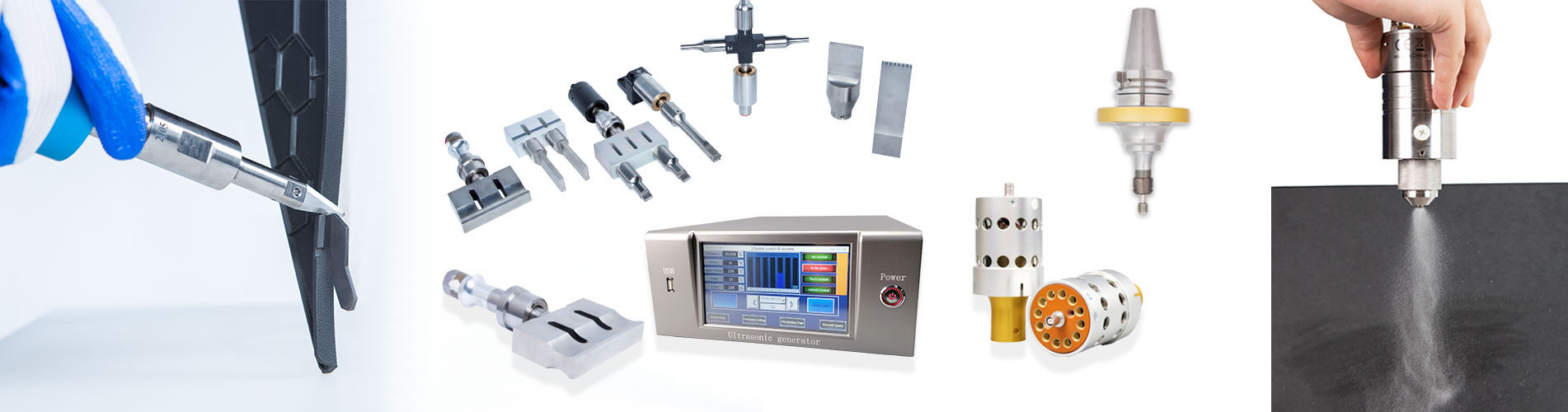
The excellent ultrasonic control technology can ensure the stability of long-term machining. Frequency scanning and power setting can be completed automatically by controller to improve productivity.
Item No.:
HS-M20Payment:
T/T, PayPal, Western UnionProduct origin:
ChinaColor:
Green SilverShipping port:
Shanghai or NingboLead Time:
40
Low Processing Forces Ultrasonic Rotary Spindle for HSK63A R8 in Aluminum Nitride
Specification:
Item No.: HS-M20
Frequency: 20kHz
Power: 500Watt
Speed: 20,000RPM
Amplitude: 10um or more
Diameter of Horn:
Milling: Φ1-Ф13mm
Drilling:Ф2-Ф6mm
Spindle: BT40 / BT50 / R8 / HSK63 / ISO / CAT
(Special spindles are made per request.)
Principle:
Ultrasonic drilling is an unconventional loose abrasive processing process. Ultrasound is a sound wave with a frequency higher than 20,000 Hz.
Ultrasonic can be generated using mechanical, electromagnetic and thermal energy sources. They can be produced from gases (including air), liquids and solids.
During ultrasonic drilling, the material is removed by micro-grinding or abrasive particle erosion.
The tool oscillates at a frequency of approximately 20 kHz by a piezoelectric sensor and an electric oscillator. The tool forces the abrasive grit to normally impact the work surface in the gap between the tool and the workpiece to machine the work surface.
The smaller the grit size, the smaller the momentum received from the tool. As the tool continues to move downward, the force acting on the larger coarse particles increases rapidly, so some coarse particles may break. Eventually, at the end of its stroke, the sand with a size greater than the minimum gap will penetrate the tool and the work surface to varying degrees.
Application:
Medical industry: Artificial crown machining
Automotive industry: Valve deburring
Die & mold industry: Surface finishing
Aerospace industry: Surface finishing
Precise ceramic industry: Roughing and finishing
Glass industry: Drilling, polishing, chamfering
Advantages:
1.Technology integration via R8 actuator system;
2.ULTRASONIC superimpositioning of the tool rotation with amplitudes up to > 10 µm;
3.Automatic frequency detection -adation, amplitude regulation and automatic feed adjustment;
4.Up to 50% reduced process forces due to ULTRASONIC allow: higher feeds, better surface finishes up to Ra < 0.2 µm, longer tool life.
Ultrasonic machining effect:
No Ultrasonic
With Ultrasonic
Previous :
Stable Amplitude Ultrasonic Drilling Process for Yttria and SapphireNext :
Rotary Ultrasonic Vibration Machining for CVD Silicon CarbideIf you are interested in our products and want to know more details,please leave a message here,we will reply you as soon as we can.
Categories
New Products
© Copyright: 2024 Hangzhou Altrasonic Technology Co.,Ltd All Rights Reserved
IPv6 network supported
Scan to WhatsApp