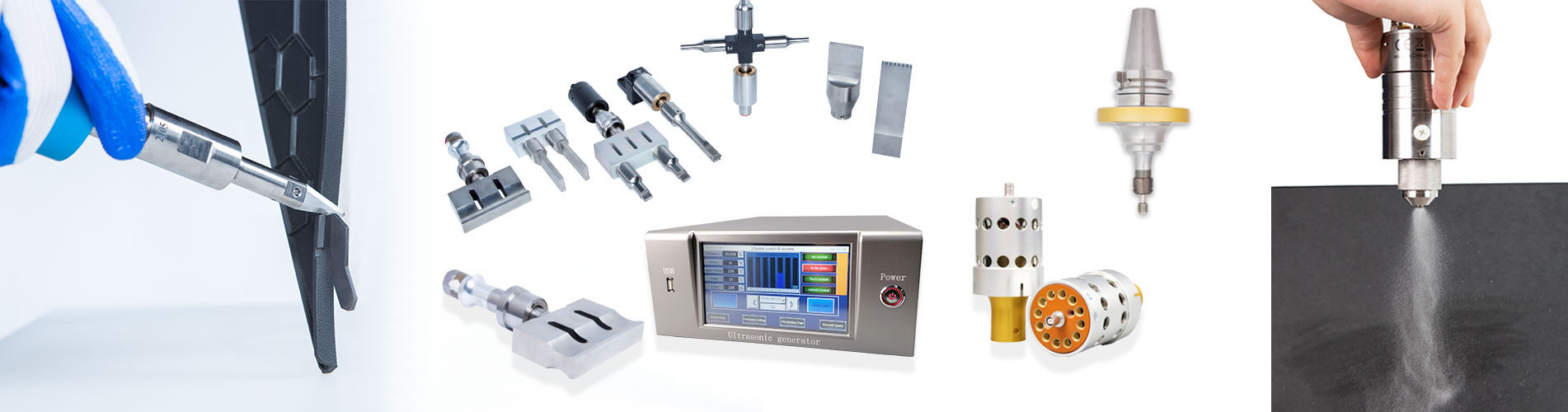
Today, biodiesel is primarily produced in batch reactors. Ultrasonic biodiesel processing allows for the continuous inline processing. Ultrasonication can achieve a biodiesel yield in excess of 99%. Ultrasonic reactors reduce the processing time from the conventional 1 to 4 hour batch processing to less than 30 seconds.
Item No.:
HSS20-3000-IPayment:
T/T, PayPal, Western UnionProduct origin:
ChinaColor:
Silver and blueShipping port:
Ningbo and ShanghaiLead Time:
15
Ultrasonic Cavitation Technology Applied to Biodiesel Processing
Specification:
Model |
HSS20-500-L |
HSS20-1000-I |
HSS20-1500-I |
HSS20-2000-I |
HSS20-3000-I |
Frequency |
20±1 kHz |
20±1 kHz |
20±1 kHz |
20±1 kHz |
20±1 kHz |
Power |
500 W |
1000 W |
1500 W |
2000 W |
3000 W |
Voltage |
220±10% V |
220±10% V |
220±10% V |
220±10% V |
220±10% V |
Temperature |
150 ℃ |
150 ℃ |
300 ℃ |
300 ℃ |
300 ℃ |
Pressure |
Normal |
Normal |
35 MPa |
35 MPa |
35 MPa |
Intensity of sound |
>10 W/cm² |
>10 W/cm² |
>30 W/cm² |
>40 W/cm² |
>60 W/cm² |
Max Capacity |
> 100M L/Min |
> 5 L/Min |
> 15 L/Min |
> 20 L/Min |
> 30 L/Min |
Material Of Tip Head |
Titanium Alloy |
Titanium Alloy |
Titanium Alloy |
Titanium Alloy |
Titanium Alloy |
Description:
Today, biodiesel is primarily produced in batch reactors. Ultrasonic biodiesel processing allows for the continuous inline processing. Ultrasonication can achieve a biodiesel yield in excess of 99%. Ultrasonic reactors reduce the processing time from the conventional 1 to 4 hour batch processing to less than 30 seconds. More important, ultrasonication reduces the separation time from 5 to 10 hours (using conventional agitation) to less than 60 minutes. The ultrasonication does also help to decrease to amount of catalyst required by up to 50% due to the increased chemical activity in the presence of cavitation. When using ultrasonication the amount of excess methanol required is reduced, too. Another benefit is the resulting increase in the purity of the glycerin.
Ultrasonic processing of biodiesel involves the following steps:
1. the vegetable oil or animal fat is being mixed with the methanol (which makes methyl esters) or ethanol (for ethyl esters) and sodium or potassium methoxide or hydroxide
2. the mix is heated, e.g. to temperatures between 45 and 65degC
3. the heated mix is being sonicated inline for 5 to 15 seconds
4. glycerin drops out or is separated using centrifuges
5. the converted biodiesel is washed with water
Costs of Ultrasonic Biodiesel Manufacturing:
Ultrasonication is an effective means to increase the reaction speed and conversion rate in the commercial biodiesel processing. Ultrasonic processing costs result mainly from the investment for ultrasonic equipment, utility costs and maintenance. The outstanding energy efficiency (click chart to the right) of Altrasonic ultrasonic devices helps to reduce the utility costs and by this to make this process even greener. The resulting costs for the ultrasonication vary between 0.1ct and 1.0ct per liter (0.4ct to 1.9ct/gallon) when used in commercial scale. Read more information about ultrasonic processing costs.
Previous :
Milk with Standard Fitting Using in Pharmaceuticals Industry for Ultrasonic Processor Sonochemistry EquipmentNext :
3000Watt Ultrasonic Assisted Oxidative Desulfurization PlantIf you are interested in our products and want to know more details,please leave a message here,we will reply you as soon as we can.
Categories
New Products
© Copyright: 2024 Hangzhou Altrasonic Technology Co.,Ltd All Rights Reserved
IPv6 network supported
Scan to WhatsApp